In technical terms, Spunbond Nonwoven fabric is actually a web composed of continuous filaments. To produce such a complex structure of fabric polypropylene which in other words is called thermoplastic is processed through a systematic and continuous process. Mathematically, a diameter of +/- 20 microns is kept while spun-melting the polypropylene granules through jets that results in fiber filaments. Those filaments are uniformly laid down into random three dimensioned web structure. The web is then presented to a calendar which thermally bonds it into a consolidated spun bond fabric. The entire production process is carried out in our state-of-the-art production unit. Every stage of the production process is monitored closely by our quality control team to ensure all the processes meet international standards of quality.
Production Process
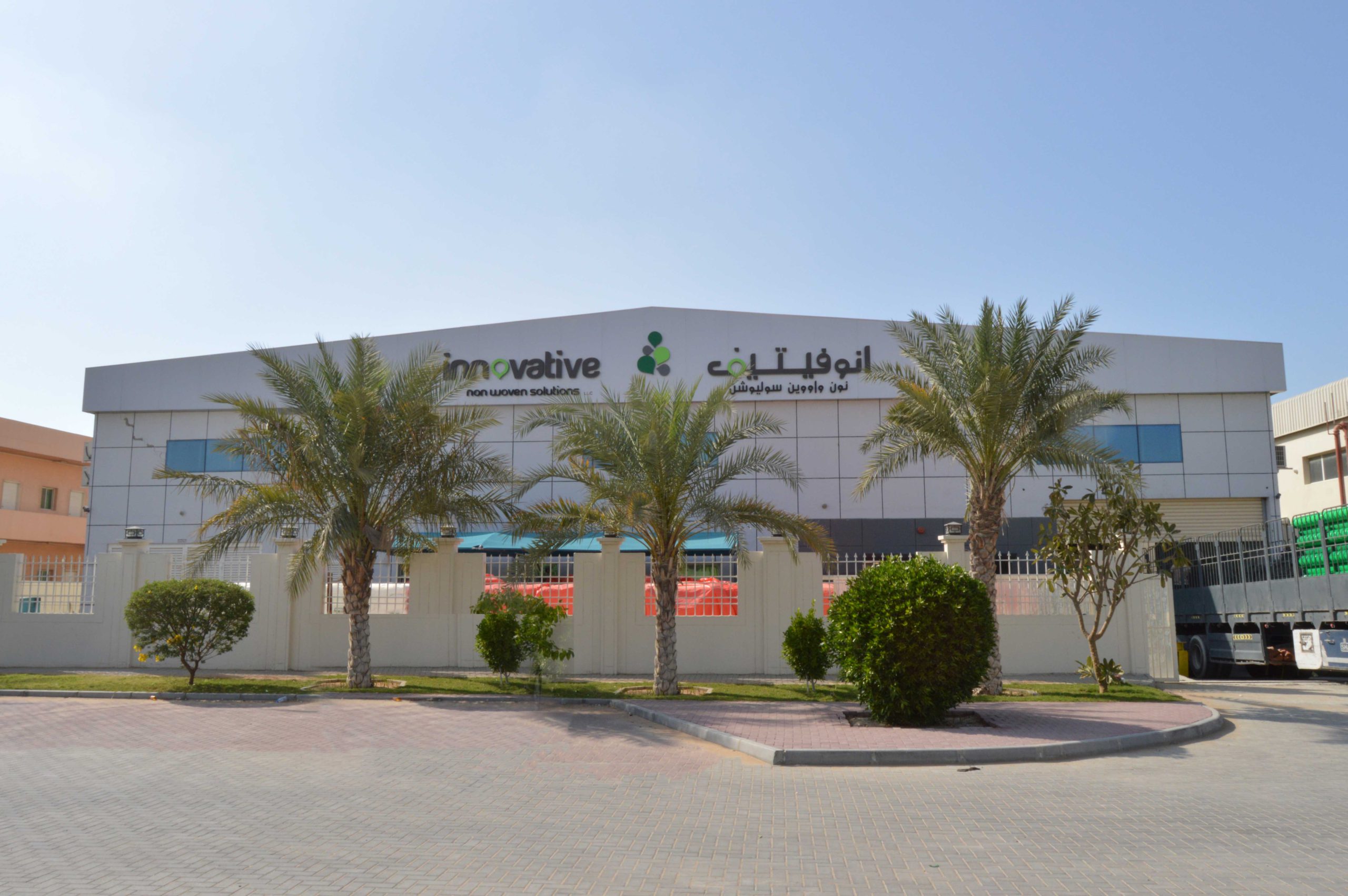
Product Details
Weight (gsm) | Width (mm) | Lenght/ Roll (m) | Roll Dia. (cm) | Weight/Roll (kg) | Core Dia. (mm) | Colors | Treatment |
“Spun bond SS” 10-150 | 60-3200 | 300-15000 | 20-120 | 5-500 | 76.2 & 101.6 | as per customer requirement | Hydrophilic U.V UV Stabilized Antistatic Flame Retardant |
“SMS” 10-70 | 60-1650 | 300-15000 | 20-120 | 5-500 | 152.4 | as per customer requirement |
Features and Benefits
General | For Hygienic | For Agriculture | For Textile |
Light & uniform weight Soft but strong |
Excellent hydrophilic properties Nontoxic & Non-irritating |
UV Resistant Creates favorable climate for plant growth |
Easy to cut, stitch heat seal Can be printed Dyed and laminated |
Machine Technical Capabilities
Capabilities (SS, SS-HI, SS-anti UV)
Production Technology | Spunbond (Double Beam technology) |
Raw Material | Polypropylene, PP color master batch, additives |
Engraving | Point Bonded |
Line width | 3200 mm (126”) |
Slitting Range | 60-3200 mm |
Weight Range | 10-150 g/m2 |
Max Filament Denies | 1.8 – 2.6 D |
Output Capacity | 6000 tons/year |
Machine Speed | 30-250m/min |
Testing Capabilities
We ensure the manufacturing of our products at a regular quality level with state of art technology testing equipment.
We perform a broad range of test in our lab to ensure what we deliver to our client’s meet the set standards and of the highest quality. We run a test such as:
- Basic Weight (g/m2)
- Tensile Strength / Elongation
- Hydrostatic head (Hydro head)
- Air Permeability
- Color
- Liquid Strike-Through Test
- Run-off Test
- Pickup
- Re-wet (wet Back)
- MFI (For Raw material)
- Moisture Content (For Raw material)
- Cantilever Test
- Petri Dish
- Fabric Thickness
SPUNBOND – MELT BLOWN COMPOSITE LINE – 1.65M (65 inch) saleable width:
- Line is capable of producing
Output:
- Basic Weight Range: 10 to 70 g/m2
- Annual Capacity: 3500 MT
Product Type:
- SMS: Spun bond – Melt blown composite fabric
- SS: Top sheet – Spun bond
Product Description
In SMS – Hydrophobic fabric, a layer of Polypropylene Melt blown is sandwiched between two Polypropylene Spun bond layers, where Melt blown functions as a barrier to fluid transmission, hence making it permanent hydrophobic.
In SMS – Hydrophilic fabric, a layer of Polypropylene Melt blown is sandwiched between two Polypropylene Spun bond layers and surfactant treatment on one spun bond layer converts the composite fabric as absorbing material, where melt blown is capable of absorbing multiple times its weight / volume.
In SS – Top sheet fabric (Hydrophilic), two layers of Polypropylene Spun bond is calendared and treated to convert hydrophobic into hydrophilic fabric.
Application
SMS – permanent hydrophobic drape able material is used in Hygiene and medical products like non-woven Barrier lag cuffs, non-woven surgical drapes & gowns, non-woven caps, comfortable face mask and many more.
SMS – Hydrophilic fabric is used in many medical applications.
- SS – Hydrophilicmaterial is used as Top sheet in Diapers & Napkins.